top of page

Back to top
Solar powered Rope making machine

A solar powered rope making machine that can be operated with a remote control. The spindles are run by different drive mechanisms that include chain, rubber belts, timing belts etc. The drive chains are then attached to a DC motor powered by solar energy. It requires just 1 person to operate using a remote control where in the traditional machine required 3.
Additional Links

The Machine with its Enclosure
The machine was developed after extensive research and prototyping. The final form is what you see here. Its enclosed in a protective shell structure that would keep it safe from the weather as well as other unaccounted for factors.
RoMa
The whole machine was named as RoMa, short for Rope Maker. The enclosure was designed with different factors in mind like ventilation, place to store the batteries and charge controllers safely, remote control and also charge it through solar power, A strong base structure was also given to handle the forces that the machine goes through.


Getting the proof concept model ready
Before the final design were developed a proof of concept model was made with a 0.25 hp DC motor to run the spindles with a V belt attachment instead of chains.
The very 1st Prototype
The machine was taken to a rope making village in Chamarajanagar located in Karnataka for testing with plastic threads as raw materials that they source from used plastic cement bags.


Nail biting moments
The result came up positive with most of the rope makers taking a liking to the machine. The buzz was vey high and the hype very real. Lot of people had gathered to see the new machine in action. There were also feedbacks that were given which was taken into account in the later models.
Dimensional design
With the conformation on the design and the feedback from the people that we tested out with, I had designed the final prototype. Even this would go through multiple iterations later on in the project. The design was conceived on Fusion 360.
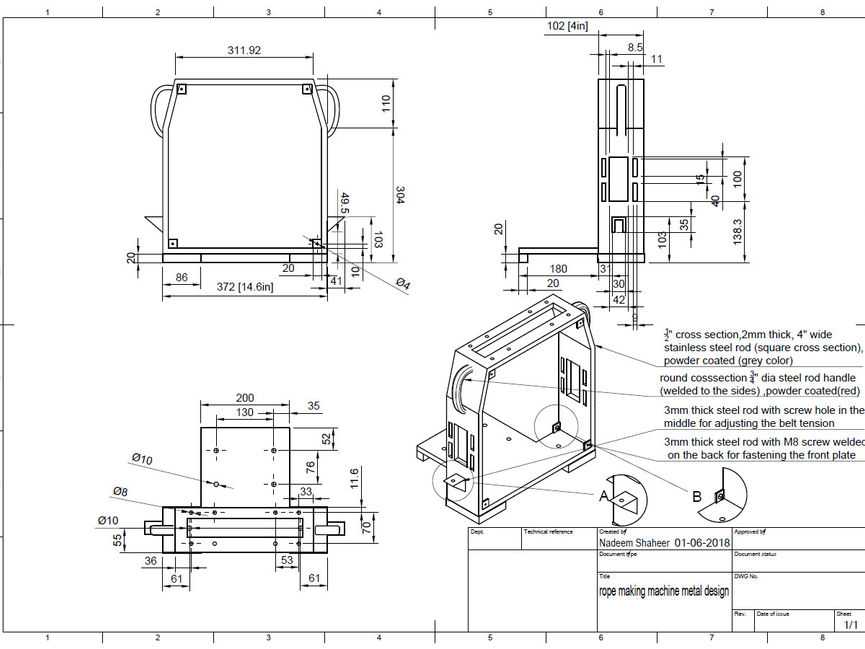

The star of the show
The main machine had 4 openings in the front, out from which 4 hooks would come out that would rotate at high speeds. When the hooks rotate anything tangled would get made to a rope due to a special techniques that the rope makers use. Usually the hooks are turned by a central gear wheel with smaller planetary gears to which the gears are attached in a traditional machine. Here we had replaced the bulky planetary wheel with chain drives attached to smaller spindles which is then attached to the motor.
3d Render
The motor for driving the spindles would be attached to the bottom plate of the machine and the smaller hooks are attached to the motor using a chain drive that would rotate it as the main motor rotates. Chain tightening mechanisms were also provided to the side hooks attachments to make the fine adjustments. Solar DC motors are very delicate when it comes to their setup and the tension in the chains has to just so right so as to not to over use the energy to run them and deplete the batteries quickly. If its loose then the wear and tear and the noise would be very high and also might lead to breakage due to the high speeds. For all this reasons a chain tension adjustor was imperative.


Final working prototype
The first slot of prototypes for testing were assembled by me in the Selco lab and was commissioned at different geographies for feedback and testing. The designs were then passed on to a manufacturer with other instructions on mass manufacturing and setting up the machines.
Test Prototypes
The testing models all had simpler base structures to keep the cost minimal. Notice the hooks that protrude out. Those had to be changed later to another design as it had to be exactly the same size and shape the rope makers were used to it in the traditional machines.


An addition to the family
Most of the rope makers welcomed the machine as part of their family. They used to do poojas and made a ceremony out of the installation process. It was quite a proud moment for me to watch my design winning a place in their hearts.
Remote control Unit
We can claim that this is the only Remote controlled rope making machine in the world right now. The remote control was added to reduce the drudgery to the rope makers.
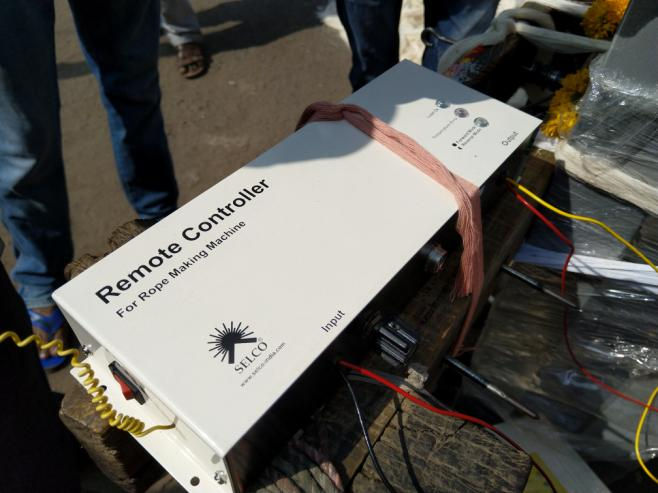
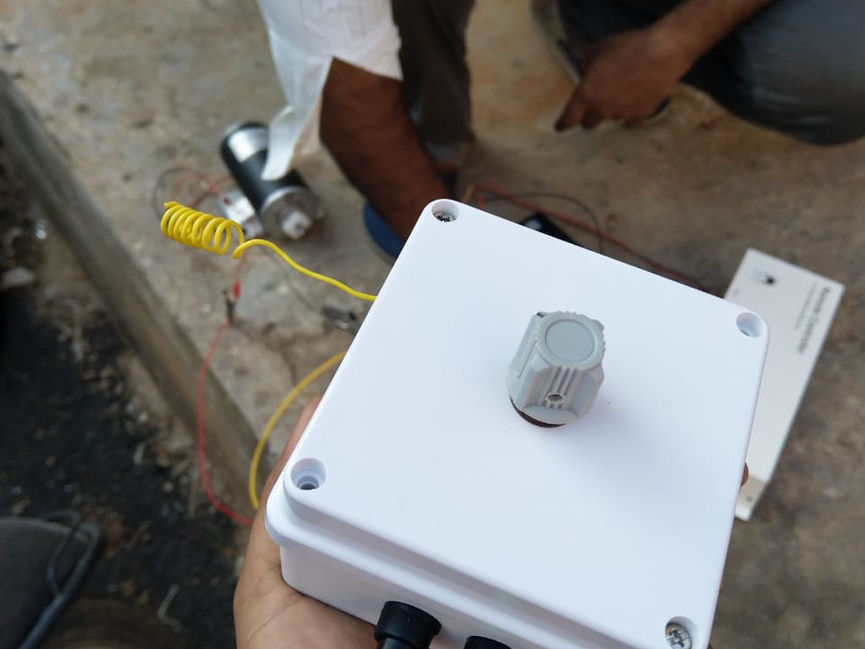
Remote controller
In the traditional rope making process there used to be a person standing next to the machine that rotates the planetary gear wheel. The machine requires to be rotated at different speeds and in two directions that would need a speed control knob as well as rotation change buttons which was provided on to the remote control. This was then hung by the rope maker by his neck as he goes around making the rope replacing the additional labor our machine.
Machine at work
Here you can see a machine that was attacehd to a moving trolley. This was done in Maharashtra as this particular rope maker did not own any property of his own and had to work in the open road. So a trolley was devised in which the machine as well as its attachments along with the batteries and the solar panels was fitted. He used to work with this in the road during the day and push it to his home during the later hours for safety reasons.

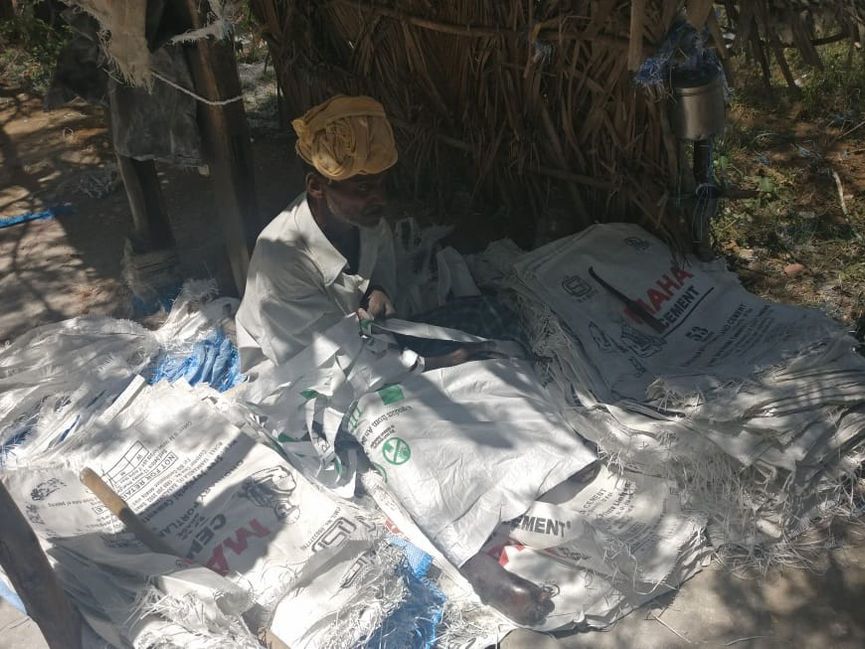
Plastic rope raw material
Plastic Rope were made from gunny bags that are sourced from used cement bags. These bags are then torn down to get long threads of plastic which is used in making the rope.
Testing in multiple villages
The machine was taken to multiple villages for testing and the results came out positive. A viable finance option was also devised for the rope makers to make the machine more accessible.
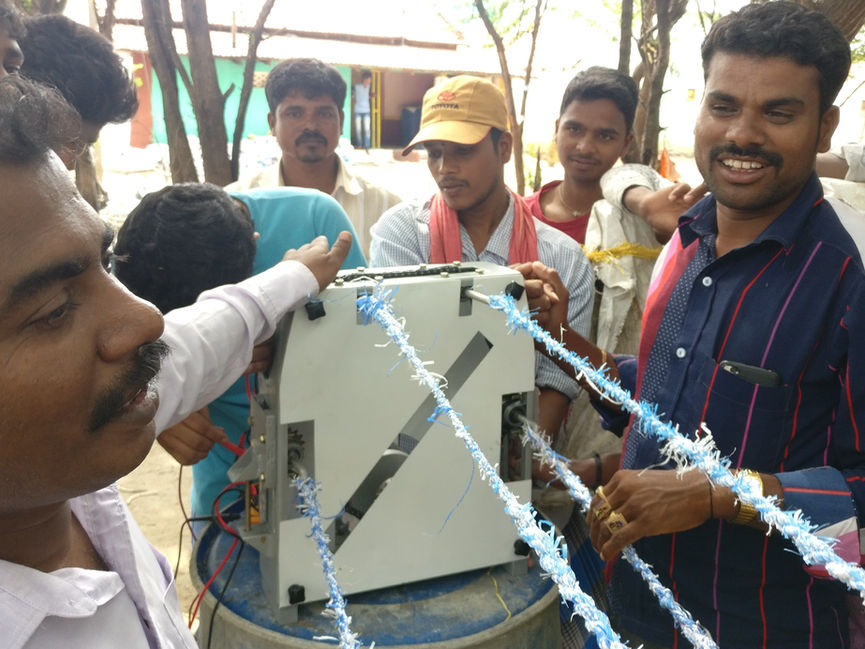
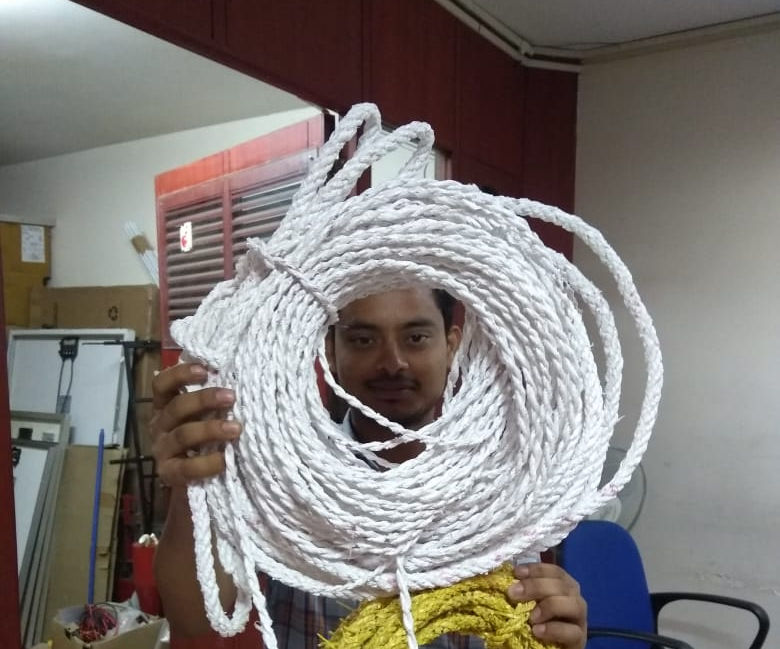
Rope made from the machine
We had compared the quality of the rope that had come out of from our machine and that from the traditional machine and the results came in favor of our machine. The rope makers were extremely happy with the result of the final product. It also reduced their drudgery and overall cost of labor as well as brought them to the modern ways of working. Here you can see one of my partner in this project Madhu flaunting the rope that was made in the machine.
Multiple geographies and testing
We had taken the machine to multiple parts of the country to understand how the people would adapt to the machine. The machine in its highest setting was able to carry out making ropes that was more than 1.5" in diameter which was quite an achievement. Here you can see the rope maker doing their job in another testing site in Maharashtra.


Smaller twin
A requirement had come from the North eastern part of India for a machine that was able to make rope with river grass. This technique requires only two spindles for making the rope and a cut down version of the machine was devised.
Me with my machine
The final product was manufactured and was inspected from my side. The first set of machines were all assembled by me to readjust the chain drive mechanism but the later batches were direct to installation
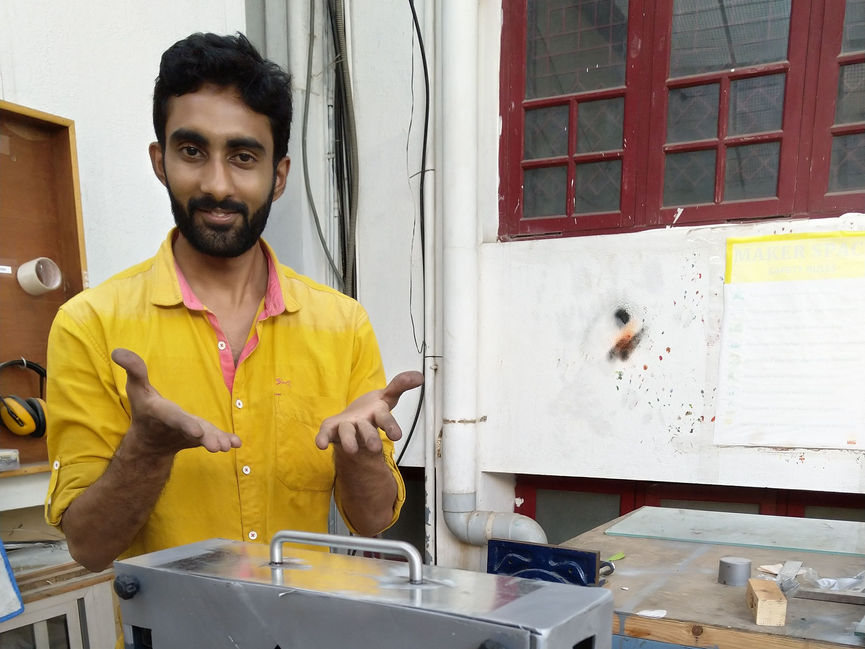

Design Constrain
The main constrain for the machine was the cost and to keep that to the minimum we had to use a 120 W DC motor instead of the usual 0.5 hp motor. The chain drive was also reworked on to increase the efficiency of the machine. It also had to be easily movable or transportable.
Machine in action
A handle along with an easily detachable base was designed for that purpose.


Another installation
This was another installation site in the rural of Tamil Nadu. The coir rope that they made with the machine can be seen in the background.
Men at work...
The team worked very cohesively to get the machine installed.

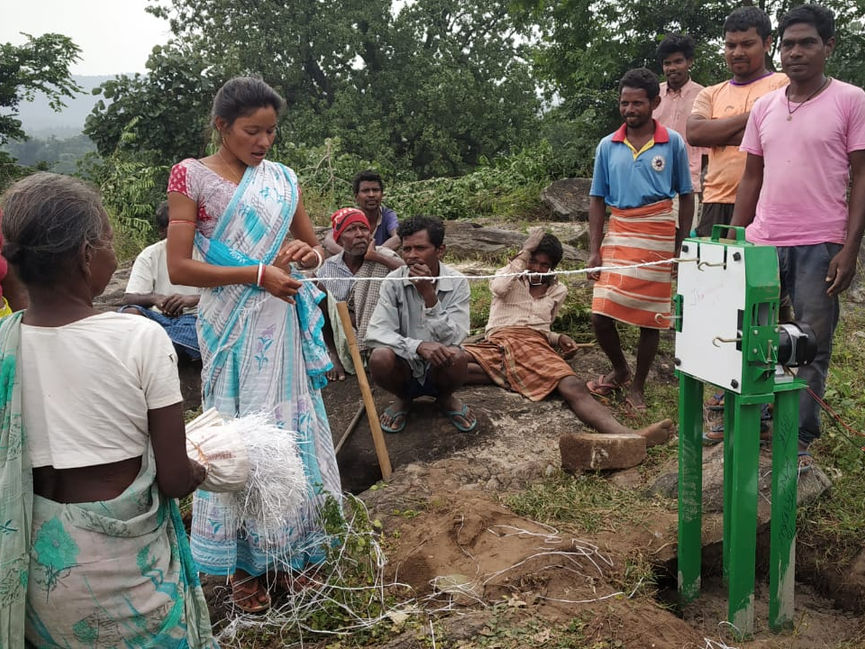
Another installation
Yet another installation...
bottom of page